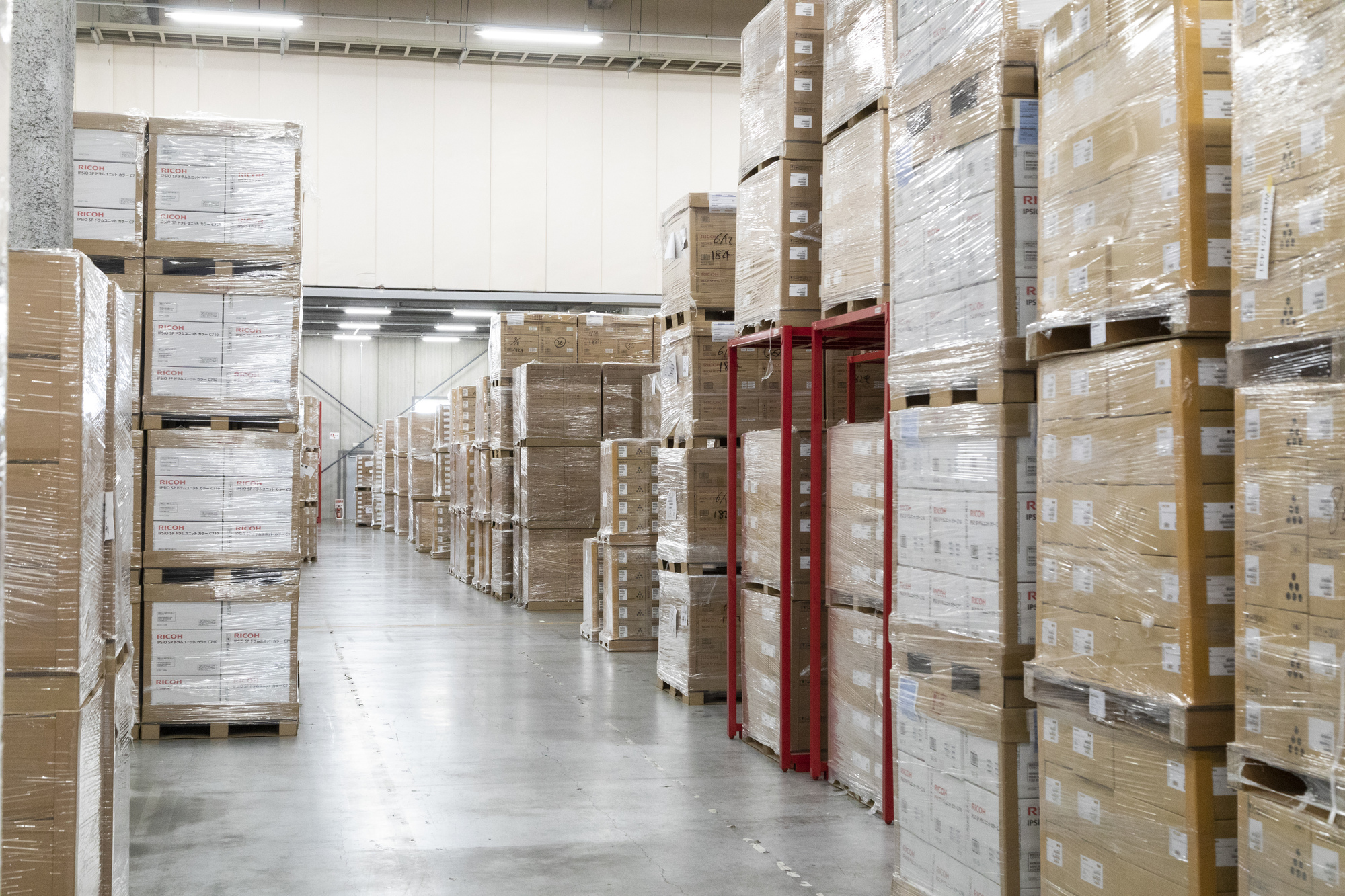
倉庫運営において、保管効率の向上は作業の生産性を左右する重要な要素です。物流量の増加や多品種少量化が進む昨今、保管スペースの最適化と在庫管理の精度向上は企業競争力にも直結します。
そこで本記事では、倉庫の保管効率が悪い場合に起こる問題点を整理したうえで、効率を高めるための考え方や具体的な改善策をわかりやすく解説します。また、保管業務の最適化に役立つ最新のシステムについても紹介していますので、ぜひ自社の倉庫改善のヒントとしてご活用ください。
目次
保管効率が悪いと起こる問題とは
倉庫における保管効率が悪化すると、さまざまな業務上のトラブルが発生します。最も顕著な問題は、在庫の出し入れに時間がかかることです。例えば、保管スペースが無駄に使用されている場合、目的の商品が見つかりにくくなり、ピッキングや出庫作業が非効率になります。
また、作業動線の悪化も深刻な問題のひとつです。必要以上に移動が発生することで作業員の負担が増し、作業ミスや事故のリスクも高まります。加えて、スペースの不足によって在庫を通路や一時保管場所に置くような事態に陥ると、火災・災害時の安全性にも問題が生じるでしょう。
このように保管効率が低い状態を放置すると、最終的には物流コストの増加や顧客への納期遅延といったビジネス全体の損失に直結します。そのため、保管効率の改善は倉庫運営において非常に重要な課題といえるでしょう。
保管効率を向上させるためのポイント
保管効率を向上させるためのポイントは以下のとおりです。
・理論上における保管場所の広さを算出する
・実際の保管場所の広さ把握する際のスペースロスを考慮する
保管効率を改善するには、まず現状の保管スペースの実態を把握することが大切です。ここからは、保管効率を向上させるためのポイントについて詳しく解説します。
理論上における保管場所の広さを算出する
倉庫の保管効率を向上させるためには、まず理論上の保管可能スペースを正確に算出することが重要です。これは倉庫の総面積や高さ、通路幅、棚の配置などを考慮し、どれだけの荷物を保管できるかを計算することを指します。
荷物のサイズや形状に応じて、最適な保管方法を選定し、それぞれの保管形態に必要なスペースを算出します。この理論値を把握することで現状の保管効率を評価し、改善の余地を明確にすることができます。
また、理論上のスペースを基に、実際の使用状況とのギャップを分析することで、無駄なスペースの特定や最適なレイアウトの検討が可能となります。このような分析を通じて、倉庫の保管効率を最大化するための具体的な施策を導き出すことができます。
実際の保管場所の広さ把握する際のスペースロスについて
理論上の保管可能スペースと実際の使用スペースを比較することで、スペースロスの有無を把握できます。スペースロスには主に「平面ロス」「高さロス」「山欠けロス」の3種類があります。
平面ロスは、通路幅が広すぎたり、荷物が適切に配置されていないことで生じる無駄な床面積です。高さロスは、倉庫の天井高を有効に活用できていない場合に発生し、棚の上部に無駄な空間がある状態を指します。山欠けロスは、棚やパレットに荷物が不均一に配置され、隙間が多くなることで生じるロスです。
これらのスペースロスを特定し、適切な保管方法やレイアウトの見直しを行うことで、倉庫の保管効率を向上させることが可能です。
倉庫の保管効率を向上させる方法
倉庫の保管効率を高めるには、単にスペースを増やすのではなく、限られた面積をいかに有効活用するかが鍵となります。そのためには、現場の状況に応じたレイアウトの見直しや、棚・ラックの活用、マテハン機器や倉庫管理システムの導入など、状況に応じたさまざまな取り組みが必要です。
そこでここからは、実際の現場で実践できる具体的な改善策について、項目ごとに詳しく解説していきます。
倉庫レイアウトを最適化する
倉庫内の動線と保管スペースを見直すことで、保管効率と作業効率を同時に向上させることが可能です。たとえば、出庫頻度の高い商品は出入口近くに配置し、ゾーンごとに分類することでピッキング作業がスムーズになります。
また、作業スペースと保管エリアを明確に分けることで、無駄な移動や混雑を減らすことができます。業務の流れに沿ったレイアウトに最適化することで、スペースの有効活用と業務の効率化が実現します。
ロケーション管理を徹底する
ロケーション管理とは、保管場所に一意の番号やコードを付けて在庫を管理する方法です。これにより「どこに何があるか」が明確になるため、ピッキングや在庫確認が迅速に行えます。
ロケーション管理を徹底することで在庫差異を減らし、作業の属人化も防げます。WMSと連携すればリアルタイムでの在庫管理も可能となるため、保管効率だけでなく精度も大きく向上するでしょう。
保管ラックを活用する
限られた床面積の中で保管能力を高めるには、保管ラックの導入が有効です。固定棚や積層ラックなど、保管物の特性や重量に応じて最適なラックを選定することで、縦方向の空間を最大限に活用できます。
また、ラックの高さや間隔を調整することでデッドスペースを最小限に抑えることができるので、結果として保管効率の向上につながります。
マテハン設備を導入する(移動ラック・自動倉庫)
マテハン設備は、保管と出荷の効率を向上させることができます。移動ラックは通路を最小限に抑えて保管密度を高められるため、限られたスペースでも大量の在庫を保管可能です。
また、自動倉庫を導入することで商品の保管・出庫を機械が自動で行い、省人化と作業精度の向上が実現します。初期投資は必要ですが、長期的には保管効率・人件費・安全性の面で大きな効果を得られます。
倉庫管理システム(WMS)を導入する
WMS(倉庫管理システム)は、入出庫、在庫、ロケーション、作業進捗などを一元的に管理できるシステムです。導入により、どこに何があるかがリアルタイムで把握できるため、作業ミスの削減や在庫ロスの防止に役立ちます。
また、WMSは作業指示や実績管理の機能も備えており、業務の標準化・効率化にも貢献します。クラウド型であれば中小規模の倉庫にも導入しやすく、コストパフォーマンスにも優れています。
以下の記事では倉庫管理システム(WMS)について詳しく説明しております。
倉庫管理システムとは?それぞれの特徴と選び方のポイントを解説
倉庫の保管効率を向上させるおすすめのシステム
倉庫の保管効率を向上させるおすすめのシステムが、シャトル型ロボットストレージシステムの「HIVE」です。前後・左右・上下の3次元移動を実現しているため、倉庫内の上部空間を有効活用することで、従来の平置き倉庫と比較して収納効率を約2倍に高めることが可能です。
「HIVE」はシャトル、コンベヤ、ラック、リフター、ボックスの5つのモジュールで構成されており、目的や倉庫の構造に応じて柔軟にカスタマイズできます。また、導入後に取扱品数や物量が増加した場合でも、シャトルやラックを追加することで拡張が容易で、メンテナンス性にも優れています。
このように「HIVE」は高密度な収納と作業効率の向上を両立させる、革新的な倉庫自動化システムとしておすすめできます。
まとめ
倉庫の保管効率を高めるには、現状の課題を把握したうえで、レイアウトの最適化やロケーション管理、ラックやマテハン機器の活用、WMSの導入などの取り組みが必要です。また、自動倉庫や保管システムの導入は、限られたスペースでも高密度かつ効率的な保管を実現させることができます。
倉庫環境に合った方法を選びつつ、長期的な業務効率化とコスト削減を実現させましょう。
関連記事