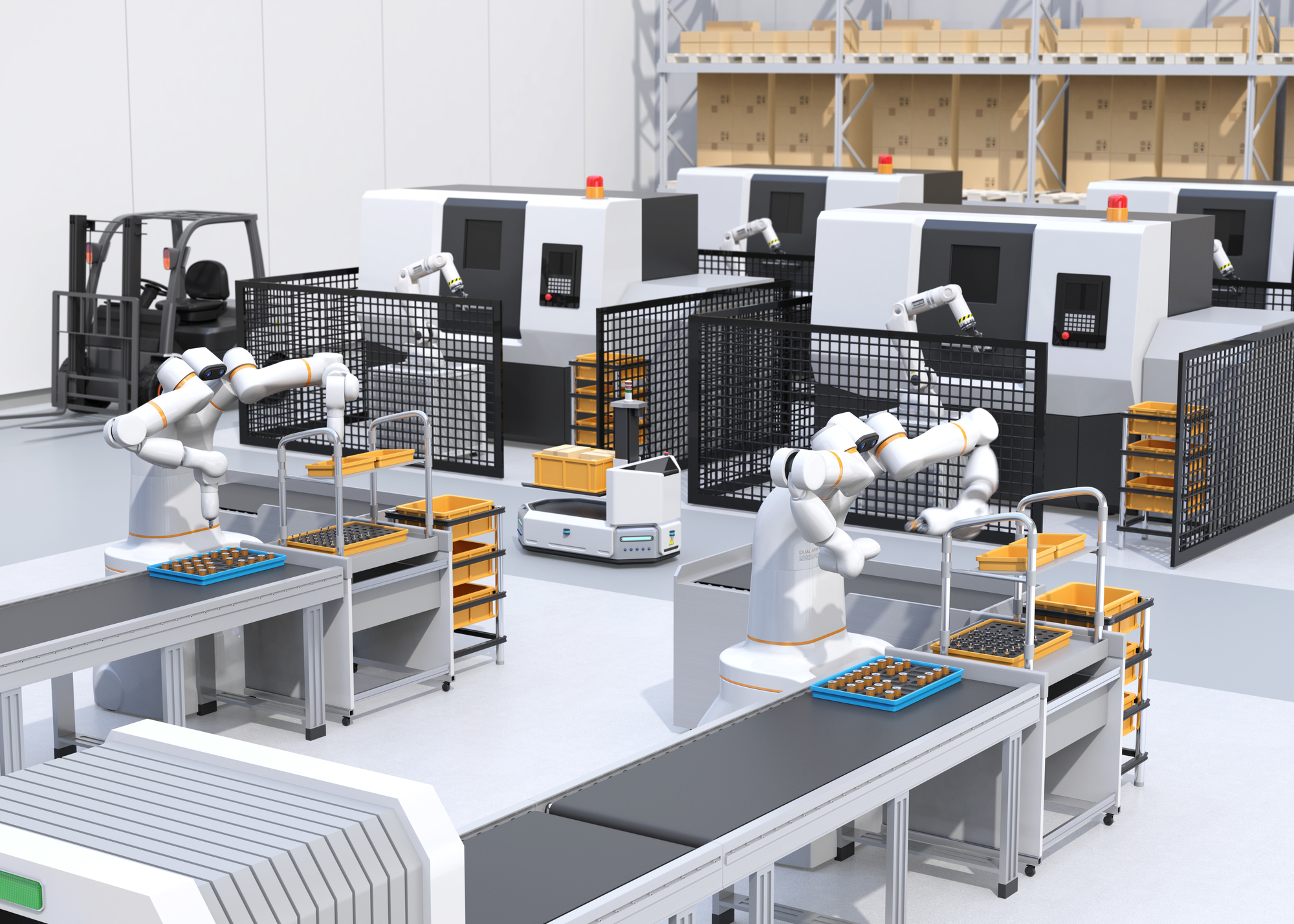
EC市場の拡大や多品種・少量出荷の増加により、物流倉庫におけるピッキング作業の重要性は年々高まっています。しかし現場では、人手不足や作業負担の増大、ピッキングミスといった課題を抱えるケースも多く、そこで注目されているのがピッキング作業の自動化です。
この記事では、そんな物流倉庫におけるピッキング作業を自動化するための代表的なシステムを紹介しつつ、それぞれの特徴や導入メリットについて詳しく解説していきます。自社に適したソリューションを見つけたい方は、ぜひ参考にしてみてください。
APTの物流システム開発ソリューション「WMS・WCS・WES」
目次
物流倉庫におけるピッキング作業の自動化とは?
物流倉庫におけるピッキング作業とは、注文に応じて商品を倉庫内から正確に取り出し、梱包・出荷するための重要な工程です。人手によって行われていたこの作業ですが、労働人口の減少やEC市場の拡大によって、作業負担の増加や人手不足といった課題が顕在化しています。
こうした背景から注目されているのが、ピッキング作業の自動化です。ピッキングの自動化とは、ロボットやセンサー、情報システムなどを活用して、商品を正確に取り出す仕組みを導入することを指します。
近年では、AIやIoTの進化により自動化の選択肢も広がっており、設備の導入コストも低下してきました。倉庫の規模や商品の特性に応じて、さまざまな自動化システムが導入されており、業務効率の飛躍的な向上が期待されています。
物流倉庫におけるピッキング自動化のメリット
ピッキング作業の自動化は、単に人の作業を機械に置き換えるだけではなく、物流全体の効率化と品質向上につながる多くのメリットをもたらします。労働力不足が深刻化する中で、生産性を維持・向上させるためには欠かせない施策となっています。
そこでここからは、ピッキング自動化によって得られる具体的なメリットについて詳しく解説します。
生産性・作業効率の向上
ピッキング作業を自動化することで、作業者が倉庫内を移動する手間が大幅に削減されます。例えば、自動搬送ロボットが商品棚ごと作業者の元へ運ぶ「GTP方式」では、作業者がその場にいながら複数の商品を効率よくピックアップできます。
また、AIやWMSと連携したシステムにより、最適な作業順やルートが自動で割り出されるため、無駄な動線がなくなります。これにより、1時間あたりの処理件数が増加し、作業効率が飛躍的に向上します。
自動化によるスピードアップはリードタイムの短縮にもつながるため、繁忙期の大量出荷にも柔軟に対応できる体制を構築できます。
人手不足の解消
物流業界では慢性的な人手不足が続いており、ピッキングのような体力を伴う単純作業への人材確保が難しくなっています。そのため、ピッキング自動化は、こうした人材不足をカバーする手段としても効果的です。
ロボットや自動化システムを導入すれば、従来なら数人が必要だった作業を1人でこなせるようになり、人手を最小限に抑えながら運用が可能になります。また、24時間稼働も可能なため、夜間の作業や繁忙期の処理量にも柔軟に対応できます。
品質の安定化
ピッキング作業における品質のばらつきは、人的ミスによって引き起こされるケースが多くあります。なかでも経験の浅い作業者による誤ピックや数量ミスは、出荷ミスや返品の原因になり、顧客満足度の低下や再作業によるコスト増加を招きます。
一方、バーコードやRFIDによる商品認識、AIを活用した画像判定、棚番号表示システムなどにより、常に正確なピッキングが可能となり、作業品質が均一に保たれます。結果として、トラブルの防止だけでなく、トレーサビリティの強化にもつながります。
コスト削減
ピッキング自動化は初期費用こそ必要ですが、長期的に見れば大幅なコスト削減が見込めます。例えば、人件費の抑制に加え、教育や研修にかかる費用、作業ミスによる再出荷・返品対応などの間接的なコストも削減されます。
また、自動化システムによって倉庫レイアウトが最適化されれば、保管効率の向上により倉庫面積を縮小でき、賃料や光熱費といった固定費も軽減可能です。自動化は一見高額な投資に見えますが、数年単位で回収可能なケースも多く、出荷件数が多い企業などでは早期に費用対効果が現れやすいメリットがあります。
物流倉庫で導入されている主なピッキング自動化システム
ピッキング作業を自動化するための技術やシステムは年々進化しており、倉庫の規模や扱う商品、運用スタイルに応じて多彩な方法を選択することができます。
そこでここからは、現在物流現場で広く導入されている代表的なピッキング自動化システムについて、それぞれの特徴と活用方法を紹介していきます。
立体自動倉庫システム
立体自動倉庫システムは、垂直方向の空間を活用して商品を高密度に収納し、自動で出し入れを行うシステムです。スタッカークレーンやシャトルが棚間を移動し、必要な商品を作業ステーションまで搬送します。
天井空間も利用しての大量保管が可能なため、倉庫の床面積が限られている現場にも適しています。全ての工程を自動化できるシステムのため、荷物や商品を大量に取り扱う企業に適している設備といえます。
自動搬送ロボット
自動搬送ロボットは、商品や棚、またはピッキング済みの荷物を自律的に移動させるロボットです。代表的な形式には、ラインを走るAGV(無人搬送車)や、センサーと地図情報を使って経路を自律判断するAMR(自律移動ロボット)があります。
これらのロボットは、作業者の近くまで商品を届けたり、ピッキング済みの荷物を次工程へ運んだりすることで人的な移動時間を削減します。ルートの柔軟性が高く倉庫レイアウトの変更にも対応しやすい点が特徴で、省人化と効率化を同時に実現する手段として導入する企業が増えています。
ロボットピッキングシステム
ロボットピッキングシステムは、アーム型のロボットが棚やコンテナから商品を自動で取り出す仕組みです。AIによる画像認識やセンサー技術を組み合わせることで、形状やサイズの異なる商品も柔軟に掴むことが可能となっています。
人手による作業と比べて、一定のスピードと精度で作業を継続できるため、品質のばらつきを抑えられるのも大きな利点です。
デジタルピッキングシステム(DPS)
デジタルピッキングシステム(DPS)は、棚に設置されたLEDランプやディスプレイを使って作業者にピッキング箇所と数量を知らせるシステムです。視覚的な指示によってミスを防ぎ、作業スピードを高めることができます。
特別なスキルが不要なため、初心者や短期間のスタッフでも即戦力として活躍できるのが特徴です。なお、DPS以外にも、間口に取り付けられたフタが開閉して効率よくピッキングできるシャッター・アソート・システム(SAS)も効果的です。
APTが提案するシャッター・アソート・システム(SAS)
倉庫管理システム(WMS)
WMS(Warehouse Management System)は、在庫・入出庫・ピッキングなど倉庫内のすべての業務を一元管理するシステムです。ピッキング自動化を本格的に運用するには、WMSとの連携が必要不可欠です。
リアルタイムで在庫状況を把握できるため、欠品や誤出荷のリスクも大幅に減少します。WMSは単体でも業務効率化に貢献しますが、他の自動化設備との連携によって真価を発揮する基盤システムです。
まとめ
物流倉庫におけるピッキング作業の自動化は、業務の効率化だけでなく、人的ミスの削減や省人化、品質向上といった多面的なメリットをもたらします。各種システムにはそれぞれ特徴があり、倉庫の規模や取扱商品によって適した導入方法は異なります。
そのため、重要なのは現場の課題や運用フローを明確にし、自社に合った組み合わせで段階的に導入していくことといえるでしょう。
関連記事