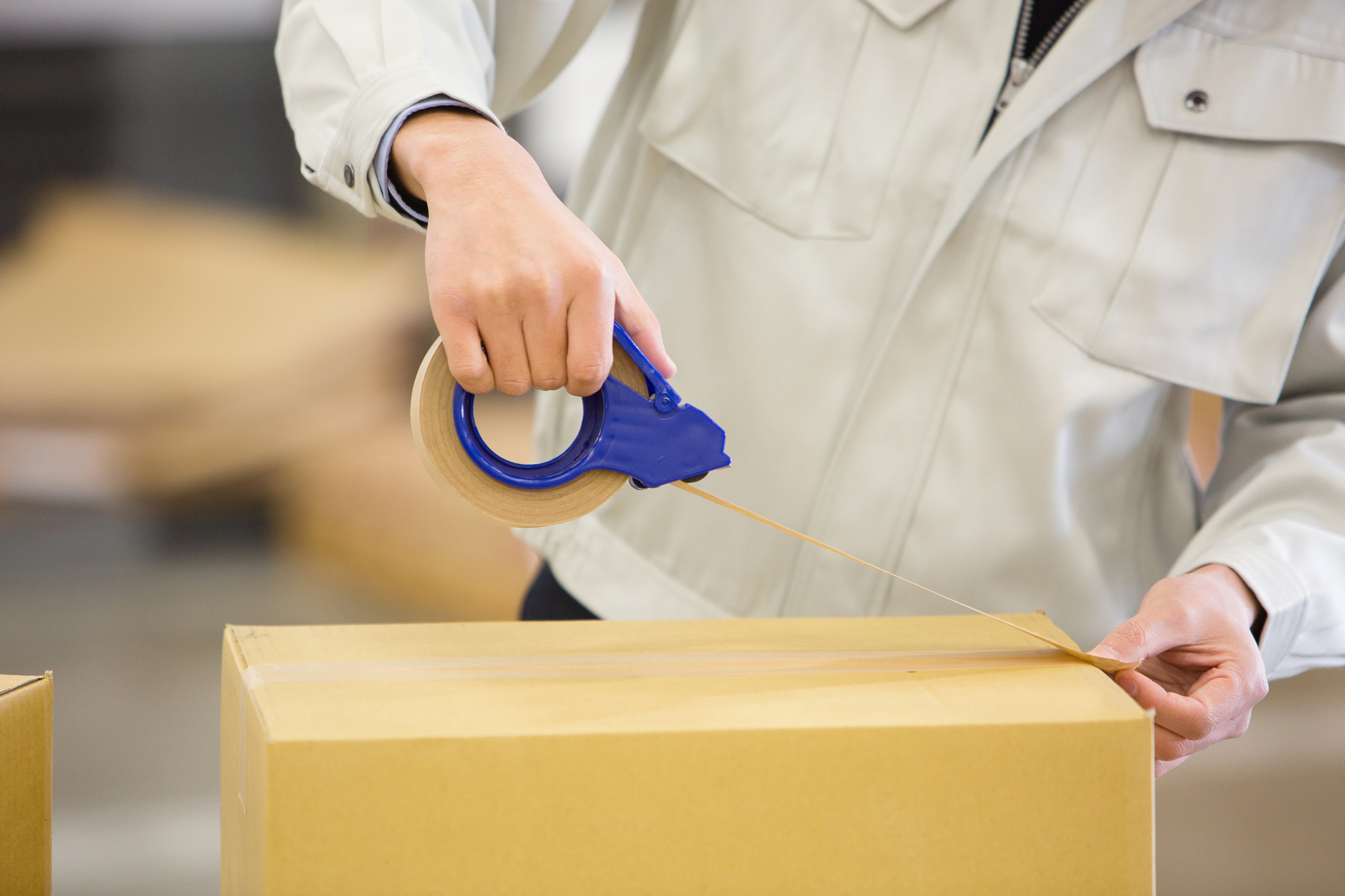
倉庫内業務の中でも出荷作業は重要な工程であると同時に、作業ミスも発生しやすい傾向にあります。出荷作業でミスが生じると誤出荷につながり、企業としての信頼も低下する恐れがあるので注意が必要です。
そのため、今回の記事では出荷作業の基礎知識を解説すると共に、出荷作業の工程でミスが生じやすい原因と改善方法について徹底解説します。また、出荷作業ミスを生じさせないおすすめのシステムも紹介しますので、ぜひ参考にしてみてください。
目次
出荷作業とは?
出荷作業とは、顧客から受けた注文の商品や荷物を倉庫から発送する作業のことをいいます。出荷作業では大量の商品を取り扱うため、作業ミスが生じると誤出荷によってクレームが発生する可能性もある重要な工程です。
そのため、出荷作業では注文通りの商品を正確に送り出す必要があるわけです。出荷作業は流通における重要な工程なので、作業ミスを生じさせないための取り組みを行わなければなりません。
出荷作業の流れ
出荷作業というのは、以下のような業務フローで作業を行います。
- ピッキング
- 検品
- 梱包
- 出荷
受注した商品というのは、出荷指示のデータを元に在庫引当を行いピッキング工程に移ります。なお、ピッキングというのは、出荷指示どおりに商品をピックアップする業務工程になります。
ピッキングした商品というのは、誤出荷を発生させないために検品工程に移ります。検品では、出荷指示と同じ商品かどうかのチェックを行うため、数量はもちろんのこと、品番やサイズなど細かい部分もチェックしていきます。
検品が終わった商品は梱包工程を経て、顧客の元へ届けるため出荷を行っていきます。このように出荷作業というのは、さまざまな業務工程を経ていくわけです。
出荷作業で起こりやすい作業ミスについて
出荷作業で起こりやすい作業ミスは以下のとおりです。
- 商品間違い
- 数量間違い
- 宛先間違い
- 付属品間違い
ここからは、出荷作業で発生するミスの原因について紹介します。出荷作業におけるミスを改善するためにも、まずはどのような作業ミスが発生しやすいのかを確認しておきましょう。
商品間違い
出荷作業で起こりやすい作業ミスの一つ目は「商品間違い」になります。商品間違いというのは、顧客が注文した商品と違う商品を出荷するという作業ミスです。なお、よくある作業ミスの原因は以下のとおりです。
- 色
- サイズ
- 品番
商品の中には同じような種類でカラーやサイズ展開が異なるケースがあるため、商品間違いを起こしやすい傾向にあります。また、品番管理をしていても入力ミスや確認ミスを起こすと、商品間違いを起こしてしまう可能性があります。
数量間違い
出荷作業で起こりやすい作業ミスの二つ目は「数量間違い」になります。例えば、商品を1個単品で注文を受けたのにもかかわらず、1パックや1ケース、1箱といった具合に単位を間違えてしまうような出荷作業ミスもあります。
その他にも、個数で入力間違いを起こしてしまうと、数量間違いのミスも発生してしまうでしょう。このように数量間違いというのは、非常に起こりやすい出荷作業ミスの一つなので注意が必要です。
宛先間違い
出荷作業で起こりやすい作業ミスの三つ目は「宛先間違い」になります。特に多い宛先間違いは「テレコ出荷」とも呼ばれており、AとBそれぞれの宛先を入れ違いで出荷してしまうようなミスが挙げられます。
このテレコ出荷は以下のようなことが原因で発生しやすいと言われています。
- 宛先表の取り間違い
- 伝票の添付ミス
テレコ出荷を起こすと顧客の個人情報も流出するため、会社としての信用を大きく下げてしまう要因になります。
付属品間違い
出荷作業で起こりやすい作業ミスの四つ目は「付属品間違い」になります。商品を出荷する際には、商品本体以外にも付属品を同梱するケースがありますが、この付属品を入れ間違えたりすることがあります。
例えば、取扱説明書や各種お知らせのチラシ、キャンペーンのノベルティなども付属品として同梱し忘れてしまうミスも発生しやすいです。中には重要な付属品を同梱する場合もあるので、付属品間違いは是正しなければならないポイントのひとつです。
出荷作業ミスを防ぐための改善方法
出荷作業ミスを防ぐための改善方法は以下のとおりです。
- 現状のチェック作業を見直す
- アウトソーシングを活用する
- システムを活用する
ここからは、出荷作業ミスを発生させないために重要な代表的な改善策について紹介します。
現状のチェック作業を見直す
出荷作業におけるミスを是正するためには、現状のチェック作業を見直すことが重要です。例えば、以下のようなポイントでミスが発生しないようなチェック作業を行う必要があります。
- 商品
- 色
- サイズ
- 数量
- 同梱物
これらはミスの起こりやすい部位なので、スタッフの役割などもきちんと周知させた上でチェック体制を構築していかなければなりません。ダブルチェック体制を構築するなど、現状のチェック作業を見直してみましょう。
アウトソーシングを活用する
出荷作業のミスを改善させる方法の一つが、アウトソーシングを活用するという方法です。自社のリソースを使って出荷作業ミスの改善をする場合、相応のコストや労力を必要とする一面があります。
しかし、出荷業務をそのままアウトソーシングを活用すれば、自社のリソースを活用することなく業務改善を図ることができます。また、外部の専門業者に委託すれば空いたリソースを別の業務に振り分けることもできるため、必要に応じてアウトソーシングを活用しましょう。
システムを活用する
さまざまな業務システムを活用することで、出荷作業のミスを改善することができます。例えば、倉庫管理システムと呼ばれる業務システムを活用すれば、入出庫管理機能が利用できるためミスを軽減させることができます。
また、ピッキングを行う際には出庫からリスト作成までをシステムで管理することができるため、ヒューマンエラーが発生しにくくなるメリットがあります。このようにシステムを上手に活用すれば出荷作業のミスを軽減できるため、アナログな運用方法からシステム運用に切り替えましょう。
以下の記事では出荷業務の効率を高める方法について詳しく説明しております。
出荷作業におすすめのシステムを紹介
出荷作業におすすめのシステムは以下のとおりです。
- 倉庫管理システム(WMS)
- 仕分けシステム(SAS)
APTでは自動倉庫を含む設備と連携した在庫管理を行える倉庫管理システム「awba」を提供しています。拡張性の高い設計をパッケージ化しているため、要望に応じて低コストで導入することができます。
また、シャッター・アソート・システム(SAS)の提供も行っており、仕分け業務を強力にサポートしています。出荷作業における仕分けミスを大幅に低減できるため、仕分け業務が必要な場合にご活用ください。
まとめ
出荷作業というのは、顧客から受けた注文通りに商品を発送する重要な作業です。出荷作業にミスが生じるとクレームに発展する可能性があるほか、場合によっては企業の信頼性を低下させてしまう原因にもなります。
そのため、ヒューマンエラーが多く発生しているような場合、早期に改善を図る必要があるでしょう。なお、WMSやシャッター・アソート・システムなどを活用することで出荷ミスを低減できるため、積極的にシステムを活用して業務改善を図りましょう。
システムの自動化や省人化をお考えの方は、APTまでご相談ください。APTでは、最先端の物流自動化ソリューションを提供しております。1社1社に合わせた柔軟なご提案をいたします。