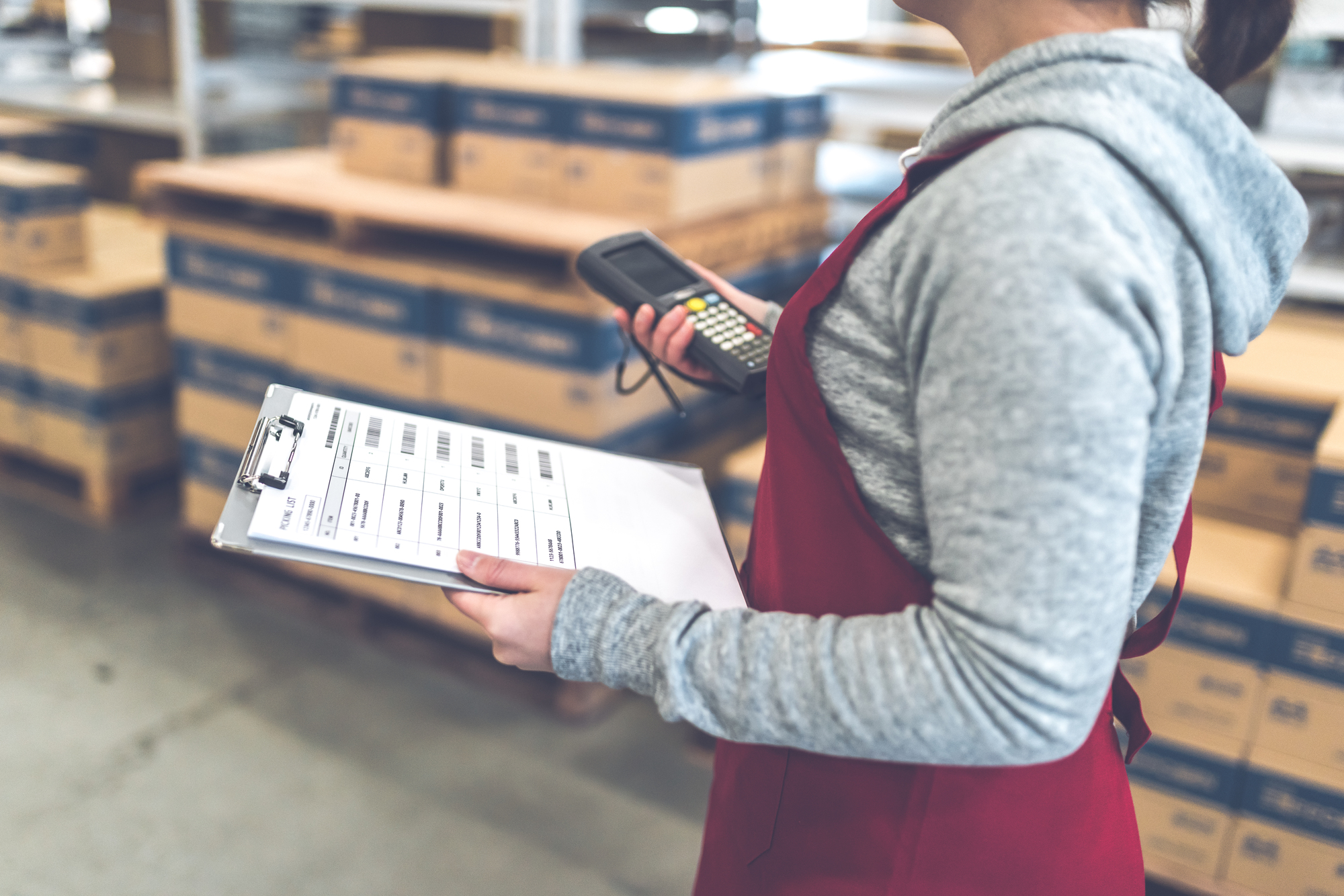
物流において誤出荷はさまざまな弊害を生むため、いかに誤出荷を発生させないかが重要と言えます。一方で、業務改善がうまくいかないと悩んでいる企業も多いのではないでしょうか。
そこで本記事では、誤出荷を防止するための対策ポイントと効果的なシステムについて解説します。誤出荷が発生してしまう原因や影響についても触れていきますので、ぜひ参考にしてみてください。
APTの倉庫リニューアル・ソリューションの資料ダウンロードはこちら
誤出荷と誤出荷率(PPM)について
誤出荷とは、出荷する商品や数量・発送先を間違えることです。間違った商品を送ったり、数量を誤って出荷したりすることで、送る相手の信用を失うリスクがあります。
物流倉庫やセンターにおける作業品質を数値で表現する際に使われるのが「誤出荷率」(PPM)です。PPMは「Parts Per Million」の略称で、直訳すると「百万分の一」を意味し、100万件の中でどれくらいの誤出荷が発生したかを数量的に表現する指標です。これは、全作業件数に対するミスの比率を示す数値で、特定の計算式によって算出されます。
PPMの算出には以下の計算式を用います。
誤出荷率(PPM)=誤出荷発生件数 / 作業件数 × 100万
例:出荷件数が10,000件、誤出荷件数が5件あったとすると、誤出荷率(PPM)は500PPMということになります。
誤出荷のパターン
誤出荷には、主に以下5つのパターンがあります。
商品の誤出荷
商品に複数のカラーやサイズがある場合、間違った品物が届けられることが多いです。お客様が望んでいない商品が届くトラブルです。
数量の誤出荷
よくある数量のミスには2つのパターンがあります。1つはまとめて注文された商品を数え間違える場合、もう1つはバラ売りの商品を1箱まとめて発送してしまう場合です。
出荷漏れ
出荷漏れも2つに分けられます。1つは複数商品を注文された際に、特定の商品を出し忘れてしまうケース、もう1つは配送時に段ボールごと商品が紛失するケースです。
宛先の誤発送
よくあるのは、配送先を取り違える「テレコ出荷」と呼ばれるケースです。送り状の貼り間違いや、配達員による仕分けミスが原因で起こります。
納品書の入れ違い
伝票などが間違た場合も「テレコ」が発生しやすいです。商品の中身に問題はなくても、個人情報が他の場所に届いてしまい、信頼性が下がるリスクがあります。
誤出荷の発生原因とは?
物流倉庫で誤出荷が発生する原因は多岐にわたりますが、主要なものとして出荷指示のミス、ピッキング作業のミス、発送時のミスが挙げられます。
出荷指示ミス
出荷指示のミスでは、誤った商品や数量の指示が出されることが原因となります。これは、システムや操作ミス、在庫管理の不備などが要因で起こり得ます。もし出荷指示段階でエラーが発生していれば、後の工程でそのミスに気づくことは難しいです。たとえば、数量、品番、コード、識別番号などの注文データに入力誤りがある場合、その誤った情報がそのまま引き継がれ、結果として間違った商品が積み込まれてしまいます。また、新旧の異なるロットを持つ商品については、出荷の順番を間違えることもあり得ます。
ピッキング作業のミス
ピッキング作業のミスは、商品の取り違えや数量のカウントミスが主な原因です。似た商品の混在や商品表示・ラベルの誤りが要因となることがあります。例えば、管理タグの間違った貼付けがあると、システム上は問題ないと判断され、そのまま出荷されることになります。また、似たような商品の取り間違い、数量のカウントミス、セット商品の一部を入れ忘れるなど、ささいな注意不足から起こるミスがあります。宛先の確認ミスは、指示書の誤読などが原因で発生することがあります。
発送時のミス
発送時のミスは、梱包作業や配送業者への引き渡し時に誤りが生じることが原因です。梱包材の不足や作業環境の問題、過労や人手不足などが要因で発生します。この段階では、ミスが起きやすいことを意識する必要があります。積み下ろしの間違いは、しばしばドライバーの責任とされがちですが、運用面の管理不備も問題として指摘されることがあります。過度な労働負荷や配送ルートの未整備が原因でミスが生じることもあり、荷積みや配送指示の改善が求められています。
これらの原因を把握して適切な対策を実施することで、物流倉庫での誤出荷を防止し、業務効率化や顧客満足度の向上に繋げることができます。
誤出荷が起きた場合のリスクや影響
誤出荷が起きた場合、様々なリスクや影響が生じます。
無駄な発送コストが増加
まず、無駄な発送コストが増加します。誤った商品が出荷された場合、返品や再出荷が必要になるため、送料や梱包費用が二度かかります。また、返品処理や再発送作業による労力も増大するでしょう。
在庫差異の発生
次に、在庫差異も生じます。誤出荷により、実際の在庫とシステム上の在庫が異なる状態が発生するので、正確な在庫管理が難しくなります。在庫差異が続くと、適切な発注や販売戦略が立てられず、業績に影響を与えることもあります。
顧客からの信頼低下
誤出荷が続くと、顧客からの自社に対する信頼が大きく低下します。誤出荷は顧客にとっては不利益な状態なので、クレームやリピート購入の減少につながります。当然、企業のブランドイメージや評判も損なわれる可能性もあるでしょう。
個人情報の漏洩
個人情報が流出する可能性もあります。顧客の個人情報が記載された伝票や書類が誤って他の顧客に届くと、情報漏洩に繋がり信頼の失墜や法的なトラブルに発展することもあります。
作業効率の低下
誤出荷が発生すると、顧客対応や返品処理、在庫確認などのイレギュラー業務が増え、本来の業務が疎かになり再度ミスが発生する可能性があります。また、ミスの原因究明のため作業履歴の追跡が必要となり、スタッフの負担も増えます。
誤出荷はこのような弊害やリスクが想定できるため、早期に改善しなければなりません。
誤出荷の防止対策6つ
誤出荷を防止するために重要な対策は以下のとおりです。
誤出荷の防止対策①:徹底した検品と出荷業務の見直し
誤出荷の防止対策②:人材育成とチームワーク向上
誤出荷の防止対策③:適切な在庫管理と整理整頓
誤出荷の防止対策④:作業マニュアルの作成と徹底で対策
誤出荷の防止対策⑤:ダブルチェック体制で検品ミスを防止
誤出荷の防止対策⑥:自動ピッキングなど出荷・検品作業にIoTを取り入れる
これらの点を事前に把握することで、実際にどのようなシステムを活用すれば良いのかを判断することができます。
誤出荷の防止対策①:徹底した検品と出荷業務の見直し
誤出荷を防止するための対策の中で重要なポイントとして、徹底した検品と出荷業務の見直しが挙げられます。
まず、徹底した検品を行うことで、商品の取り違えや数量のカウントミスを防ぐことができます。検品作業を二段階にすることで、ミスの見落としを減らすことができるほか、バーコードやQRコードを活用して商品の確認を行うことで、効率的かつ正確な検品が可能になります。
次に、出荷業務の見直しを行うことで、業務プロセスの効率化や改善が図られます。出荷指示やピッキング作業、梱包・発送作業などの各工程を検証し、問題点や改善点を明確にすることが重要です。
これらの対策を実施することで、誤出荷のリスクを最小限に抑えることができるため、顧客満足度や業務効率の向上に繋がるでしょう。
誤出荷の防止対策②:人材育成とチームワーク向上
誤出荷を防止するための対策として、人材育成とチームワーク向上が重要なポイントです。
人材育成では、従業員が業務内容や注意点を十分に理解していることが求められます。定期的な研修や教育プログラムを実施し、従業員のスキル向上を図ることで、ミスの減少や効率的な作業が期待できます。また、新人教育やメンター制度を導入することで、経験豊富な従業員から新人への知識伝達がスムーズに行われるため業務改善に繋がります。
またチームワーク向上によって、従業員同士のコミュニケーションが円滑になり、作業効率やミスの回避が図られます。定期的なミーティングや情報共有を行って問題点や改善提案を積極的に議論することで、業務改善に繋げることができます。その他にも、チームビルディングや意見交換の場を設けることで、互いの理解を深め協力的な雰囲気が醸成されます。
これらの対策を実施することで、誤出荷のリスクを最小限に抑えることができ、業務効率や顧客満足度の向上に繋がります。
誤出荷の防止対策③:適切な在庫管理と整理整頓
誤出荷を防止するための対策として、適切な在庫管理と整理整頓が重要なポイントです。
適切な在庫管理は、商品の出荷指示ミスや在庫差異の発生を防ぐために必要です。定期的な在庫点検やリアルタイムの在庫情報共有を行い、商品の在庫状況を正確に把握することが求められます。また、在庫管理システムの導入やバーコード・QRコードを活用した商品識別により、在庫管理の精度が向上し、誤出荷のリスクを低減できます。
整理整頓は、倉庫内でのピッキングミスを防ぐ上で欠かせません。商品の分類や棚卸しを適切に行い、類似商品が混在しないように注意することが重要です。また、明確なラベリングや棚番号の表示を行い、商品の特定が容易になるよう工夫をすることが求められます。さらに、5S(整理、整頓、清掃、清潔、躾)活動を取り入れることで、倉庫環境の改善が図られ、作業効率やミスの回避が期待できます。
これらの対策を実施することで、誤出荷のリスクを最小限に抑えることができ、業務効率や顧客満足度の向上に繋がります。
誤出荷の防止対策④:作業マニュアルの作成と徹底で対策
誤出荷を防ぐには、倉庫内業務フローをマニュアルかし、作業手順やルールを明確化し徹底することが大切です。
例えば、納品書の間違いを防ぐためには、出荷の準備を始める際に送り状、納品書、出荷指示書を一緒にしておくと良いでしょう。
また、テレコ出荷(送り状と納品書の不一致)は、これらの最終チェックを丁寧に行うことで防ぐことができます。各工程でエラーが起きにくいように工夫し、万が一のミスが発生しても次の工程で誤出荷を防ぐ体制を作り、ルールの徹底と遵守に努めましょう。
誤出荷の防止対策⑤:ダブルチェック体制で検品ミスを防止
チェック体制を整備して誤出荷を防ぐことが重要です。特に効果的なのはダブルチェック体制の採用です。これにより、各工程でミスを発見しやすくなります。
ただし、デメリットとしては、追加の人件費が必要になることと、ダブルチェックを行う人が「ミスは起こらない」という前提でチェックすることにより、実際のミスを見落とすリスクがあります。注文全体におけるミスの割合は非常に少ないため、連続してミスがない状態が続くと、チェックする側の注意力が低下し、ミスを見逃す可能性が高まります。
誤出荷の防止対策⑥:自動ピッキングなど出荷・検品作業にIoTを取り入れる
人の手作業に依存するとヒューマンエラーの完全な排除は難しいので、ルールの厳守や定期的な見直しに加えて、IoTツールへの積極的な切り替えにより作業効率の向上と物流品質の改善が可能です。
物流倉庫で誤出荷を防止できるおすすめシステムを紹介
物流倉庫において誤出荷を防止できるおすすめシステムは以下のとおりです。
- バーコード・QRコードを活用した管理システム
- 倉庫管理システム(WMS)
マニュアルでの対策だけではなく、上記のようなシステムを活用することで誤出荷を防ぐことが可能です。
バーコード・QRコードを活用した管理システム
物流倉庫で誤出荷を防止できるおすすめシステムとして、バーコード・QRコードを活用した管理システムが挙げられます。
バーコード・QRコードを活用した管理システムは、商品の特定や在庫管理を効率的かつ正確に行うことができます。各商品にバーコードやQRコードを貼付し、ピッキング作業時にバーコードリーダーやスマートデバイスでコードを読み取ることで、商品の識別が容易になります。これにより、商品の取り違えや数量のカウントミスが大幅に減少し、誤出荷のリスクが低減されます。
また、このシステムを導入することで作業員が手動で商品情報を入力する手間が省かれるため、作業時間が短縮されて生産性が向上します。これにより、物流倉庫での誤出荷を防止することができます。
倉庫管理システム(WMS)
物流倉庫で誤出荷を防止できるおすすめシステムとして、倉庫管理システム(WMS: Warehouse Management System)が挙げられます。
WMSは、在庫管理やピッキング作業、出荷業務などの一連の倉庫業務を効率化し、正確に行うことができるシステムです。商品情報や在庫状況がリアルタイムで管理されるため、適切な在庫管理や出荷指示が可能になり、誤出荷のリスクを低減できます。
なお、倉庫管理システムを導入することで、物流倉庫での誤出荷を防止することで、業務効率や顧客満足度の向上にも繋がります。
まとめ
物流倉庫では多くのスタッフが作業をするため、出荷指示のミスやピッキングミスなど、さまざまな要因が相まって誤出荷につながってしまいます。ただし、誤出荷は物流企業にとって発送コストの増加や在庫差異、顧客満足度なども低下するため早期に改善しましょう。
なお、誤出荷を防止するためには、バーコード・QRコードを活用した管理システムや倉庫管理システム(WMS)などを活用していくことをおすすめします。
APTでは、倉庫コンサルティングを実施しております。お客様の倉庫状況、お悩み、ご要望をヒアリングして1社1社に合わせた柔軟なご提案をいたします。お気軽にご相談ください。
関連記事
物流品質の指標「誤出荷率」の計算方法から改善ポイントを徹底解説
仕分けミスを防ぐためには?発生原因と防止方法をご紹介