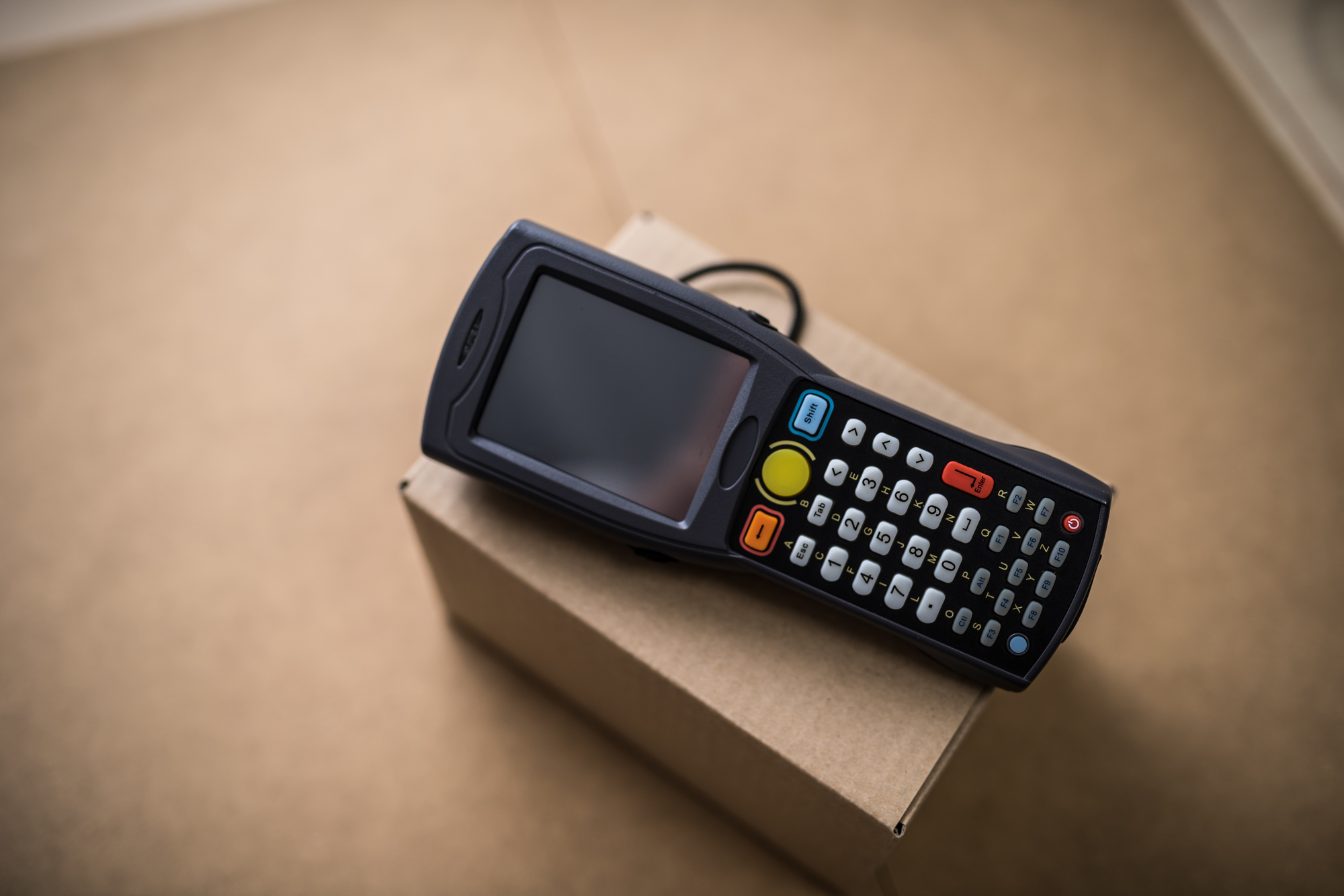
出荷指示に従い商品を取り出すピッキング作業は、正確性が求められることはもちろんのこと、作業スピードも重要な要素です。一方、ピッキングは、人が作業する工程で属人化しやすい傾向にあるため、効率化を目指している企業も多いのではないでしょうか。
そこで本記事では、ピッキングをさらに効率化させるためにはどのような施策があるのかを解説します。効果的な改善策を実施することによって、作業の効率の向上以外、人的ミス(いわゆるヒューマンエラー)の削減にもつながるため、ぜひ参考にしてみてください。
APTの「リニューアル・ソリューションのご紹介」の資料ダウンロードはこちら
目次
ピッキング作業とは
ピッキング作業は、倉庫内の商品を出荷指示書や伝票(ピッキングリスト)に基づいて、必要な数量だけ選び出していく仕事です。選び出した商品を台車などに積んで、梱包や検品を担当する作業者に引き渡すのが一般的な手順です。
ピッキングの種類
ピッキング作業には、摘み取り式と呼ばれるシングルピッキング、種まき方式と呼ばれるトータルピッキングの2種類が存在します。
取り扱う商品や倉庫内環境によっても変わるため、ここではこれらピッキングの種類について解説します。
シングルピッキング(摘み取り式)
シングルピッキングとは、注文ごとに商品を取り出してピッキングを行う方法で、別名「オーダーピッキング」や「摘み取り式」とも呼ばれています。注文毎にピッキングをするため、オーダーの数が少なくSKU(ストックキーピングユニット)の多い作業に適した方法といえます。
少量多品種を取り扱う「通販」や「ネット通販(EC)」に向いているピッキング方式で、主にBtoC関連の物流倉庫で多く採用されています。
トータルピッキング(種まき式)
トータルピッキングとは、複数ある出荷オーダーの商品をまとめてピッキングした後、仮置き場で出荷別に仕分けを行う方法です。別名で「バッチピッキング」や「総量ピッキング」「種まき方式」とも呼ばれています。
同じ商品が複数の出荷先にまたがるようなケースに効果的なピッキング方式で、出荷件数が多くSKU数が少ない場合に有効な方法です。
ピッキング作業における課題
倉庫内業務の中でも、ピッキングはより効率化を求められる工程です。しかし、属人化もしやすい傾向にあるため、さまざまな課題を抱えてしまうケースも多いでしょう。
そこでここからは、ピッキング作業では「どのような課題に直面しやすいのか」具体的に解説します。
移動時間がかかる
ピッキングを行う際には、商品が保管されている棚まで移動して取り出さなければなりません。そのため、倉庫内が広くなっていくにつれて移動時間が増えていくため、ひとつの商品をピッキングするだけでも時間がかかってしまう傾向にあります。
また、倉庫の通路が狭いケースや、整理整頓がされていない環境で商品棚まで移動する場合、通常よりも余計に時間がかかってしまうことも多いです。このように、移動時間のロスというのは、ピッキング作業において大きな課題のひとつといえるでしょう。
商品探しに時間がかかる
ピッキング作業では、出荷指示に従って商品をピックアップしなければなりません。しかし、商品の保管場所リストが明確でなかったり、わかりにくい場所に商品が保管されていると、商品探しに時間がかかってしまう傾向にあります。
また、本来あるべき場所に商品が保管されていない場合、無駄に商品探しに時間を使ってしまうことも多いでしょう。そのため、商品探しも効率化を求めなければならない課題のひとつとして捉えることができます。
ヒューマンエラーの発生
人がピッキング作業をする場合、人的ミス(ヒューマンエラー)をいかに無くすかが課題といえます。例えば、取り出すべき商品を間違えてしまったり、数量を間違えてしまうなど、ヒューマンエラーの原因は多肢に渡ります。
このように、人が作業する場合は人的ミスの発生が想定できるため、スタッフの教育はもちろんのこと、Wチェック体制を強化する必要もあるため、大きな課題のひとつといえるでしょう。
ピッキング作業を効率化するためのポイント
物流業務の中でも、ピッキング作業の効率化は非常に重要なプロセスのひとつです。ここを改善することによって人的ミスも大幅に削減できるため、積極的に改善を図りましょう。
そこでここからは、ピッキング作業を効率化して人的ミスを減らす具体的な方法について解説します。
整理整頓の徹底
倉庫内が綺麗に管理されていない場合、作業効率は大幅に低下します。また、スタッフの通行を妨げてしまうようなケースも発生するため、転倒など怪我のリスクまで抱えてしまうことになるでしょう。
- 整理
- 整頓
- 清掃
- 清潔
- 躾
不要なものを処分すること
使う物品の位置を適切に配置すること
ゴミや汚れを取り除くこと
整理・整頓・清掃の3つを維持すること
従業員が上記4つを守るよう教育すること
以上のことからも、倉庫内の整理整頓を徹底していくことは、作業効率を上げるために必ず必要といえます。5S活動(整理・整頓・清掃・清潔・躾)を徹底して、倉庫内を綺麗に保つところから始めましょう。
マニュアルの明確化
ピッキング作業を属人化させずに品質を平滑化させるためには、作業マニュアルを明確にする必要があります。どのような手順でピッキングを進めていくのか、手順や方法をわかりやすくまとめていくことが重要です。
また、ピッキングリストは複雑にしてしまうと作業効率が落ちてしまうため、より簡潔にわかりやすくまとめることによって、スタッフの作業効率は向上するでしょう。
ロケーションの見直し
ピッキング作業では、商品を取り出す際の移動時間にロスが生じやすいため、ロケーション管理が非常に重要です。より効率的に商品をピッキングするためにも、最適な倉庫レイアウトにしましょう。
保管棚のレイアウトや動線などを考慮することによって、倉庫内の移動も短縮できます。また、作業員の労力軽減にもつながるため、ロケーションの見直しをすることによって、ピッキング作業を効率化できるでしょう。
ピッキングシステムの導入
ピッキングリストを作成して人が作業する場合、効率化にも限界があるほか、属人化しやすい傾向にあります。そのため、ピッキングシステムを導入することによって、作業効率は大幅に向上します。
代表的なピッキングシステムの種類は以下となります。
・デジタルピッキングシステム(DPS)
・プロジェクションピッキングシステム®(PPS)
・ボイスピッキングシステム
・デジタルアソートシステム(DAS)
・スマートフォン・タブレットピッキングシステム
なお、近年ではバーコードを利用するピッキングシステムが主流です。ただし、音声ピッキングシステムやデジタルピッキングシステムなど、さまざまなタイプが存在するため、自社の環境に合ったものを導入しましょう。
※「プロジェクションピッキングシステム」は株式会社アイオイ・システムの登録商標です。
ピッキングシステムについてはこちらの記事でご紹介しています。
ピッキングシステムとは?種類と選び方について解説
WMSの導入
倉庫管理システム(WMS)を導入することによって、入出庫にかかるロケーションまでデジタル管理できるようになります。アナログ管理とは違って、リアルタイムで保管状況などの情報共有もできるため、ピッキング作業の効率は大幅に向上するでしょう。
また、システム管理になるため、アナログ管理で多く発生していた「数量」や「商品」の間違いなど、ヒューマンエラーも防ぐことができます。
WMSについてはこちらの記事でご紹介しています。
WMSとは ?基幹システムとの違いやメリットを紹介
まとめ
倉庫内作業の中でもピッキングは重要な工程ですが、人が作業するため商品探しや移動時間のロス、人的ミス(ヒューマンエラー)などさまざまな課題があるといえます。そのため、適切な改善策を実行して業務内容の改善を図りましょう。
なお、有効な改善策としては、整理整頓や作業マニュアルの策定にはじまり、ロケーションの見直しやピッキングシステムおよびWMSの導入など多彩な方法がありますので、自社にとって取り組みやすい内容から実現させましょう。