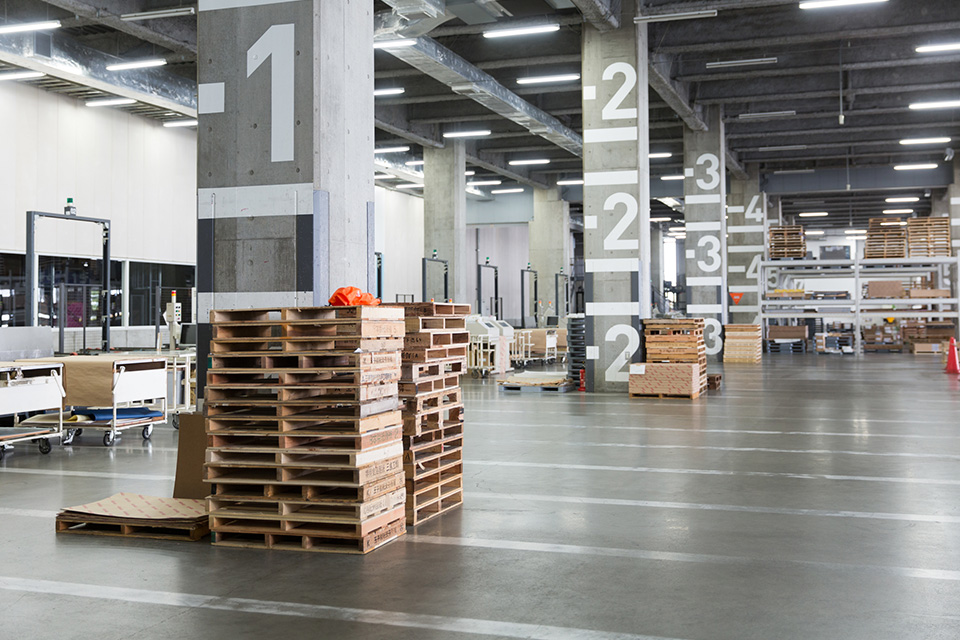
限られた倉庫内のスペースで作業効率を最大化するためには、既存のレイアウトを見直してみることが重要です。ただし、すでに運用されている倉庫の場合、どのようなレイアウト変更で改善をすればいいのか分からないというケースも多いのではないでしょうか。
そこで本記事では、そもそも倉庫レイアウトとは何か?を解説するとともに、レイアウト改善の考え方や具体的な方法について徹底解説します。改善が必要な理由についても紹介しますので、ぜひ参考にしてみてください。
APTの「リニューアル・ソリューションのご紹介」の資料ダウンロードはこちら
目次
倉庫レイアウトとは?
倉庫におけるレイアウトは、限られた倉庫内の有効面積において、その規模や業務内容に合わせて商品の保管場所や方法を決めることをいいます。例えば、商品を保管するロケーションを業務効率上、最適な位置にすることも倉庫レイアウトの基本です。
また、倉庫内の通路や動線についても、業務効率を意識してレイアウトすることが重要です。これらを意識して設計された倉庫レイアウトは業務効率が改善するため、最適な倉庫運営を行うことにつながります。
倉庫レイアウトの改善が重要な理由
倉庫を運営する上で、レイアウトを改善することが非常に重要です。新たにレイアウト設計を行う際には、まず改善することによるメリットや、その重要性について正しく理解しておくことが必要です。
そこでここからは、どうして改善が重要なのか?その理由について具体的に解説します。
各作業の効率化が可能
改善する上で重要な理由の一つが、業務の効率化を実現できるということです。反対に効率的でない場合、無駄な移動や作業が増えてしまいデメリットが多くなってしまいます。
しかし、業務プロセスを意識した倉庫レイアウトにすることで、移動による時間的ロスや作業の手間が改善されます。そのため、業務の効率化を図ることになり、生産性の向上も実現できます。
コスト削減が期待できる
レイアウトの最適化によって業務効率が改善するため、物流コストの削減が期待できます。従来と同じ作業量でも短い時間で効率的に行えることで、必要になる人員配置の数も減らすことが可能です。
また、保管効率も向上することで、無駄にしていた面積を削減することになります。これにより、従来よりも保管コストを削減可能なので、より効果的な倉庫運営を実現させることができるでしょう。
保管効率の向上を期待できる
適切な倉庫レイアウトを行うことで商品の出し入れがスムーズになり、棚の中の商品を探す時間が短縮されます。これにより在庫管理が容易になるだけでなく、出し入れ時に商品を落としたり、何かにぶつけるといったリスクも減り、商品の品質を保つことができます。さらに、無駄なスペースが減ることで、保管スペースを最大限に活用できます。
業務ミスや事故を予防できる
倉庫レイアウトを改善することで、業務のミスや事故を予防できるという点も挙げられます。レイアウトに問題がある場合、搬送業務の際に接触事故などを起こしてしまう可能性があります。
しかし、正しく整備された倉庫レイアウトの場合、このような業務ミスや事故を未然に防ぐ効果が期待できます。業務の安全性を向上させるという観点からも、レイアウト設計は非常に重要ということです。
簡単にレイアウト変更ができないため
倉庫レイアウトの改善が重要な理由の一つに、簡単にレイアウト変更ができないということがいえます。一度決められたレイアウトは、基本的に長い期間そのまま運用されることになります。
商品を保管する棚や通路の確保など、これらの位置変更はすぐに変更できるものではありません。そのため、効率的でないレイアウトというのは、長い期間運用されてしまう可能性があるということです。
そのため、倉庫は最適なレイアウトに改善して運用していく必要があるというわけです。
倉庫レイアウトを改善するための考え方
倉庫レイアウトを改善するに当たり、以下のような考え方を持ってレイアウト変更をすることが重要です。
ABC分析
ABC分析とは、売上や出荷頻度などの評価軸を決めた上で、A、B、Cと多い順にグループ分けをして優先順位を決める方法です。商品に評価軸が定まることで、保管場所や動線を最適化させることができます。
Aグループ商品
流動性・出荷頻度が高い商品。頻繁に商品を取り出すため、作業効率を優先する。
Bグループ商品
流動性・出荷頻度が平均的な商品。作業効率と保管効率のバランスを考えて保管する。
Cグループ商品
流動性・出荷頻度が低い商品。取り出す回数が少ないため、状態が悪くならないように保管効率を優先する。
最も取り出しが頻繁なAグループの商品は、出入り口やメインの通路に近い場所に配置することで、ピッキング(商品の取り出し)の効率を向上させることができます。
ロケーション管理
ロケーション管理を前提にしたレイアウトにすることも重要です。ロケーション管理は、どこに何が保管されているのかを明確に管理する方法で、より緻密な商品管理をすることができます。
棚で商品を管理している場合、1段ずつにロケーションを割り当てます。この方法のメリットは棚の番号で商品の正確な位置をすぐに把握でき、ピッキングが効率的に行うことです。
ABC分析とロケーション管理を活用しつつ、レイアウトを決めることが重要です。
効率的な作業を実現するための倉庫レイアウトのポイント
最適な倉庫レイアウトに改善するためには、以下の手順を参考に設計してみましょう。
・課題を明確にする
・業務工程を確認する
・倉庫レイアウトを決める
・保管場所を決める
ここからは、具体的な手順とその中身について紹介します。
課題を明確にする
倉庫レイアウトを改善する際には、現状で抱えている問題点や課題を事前に明確にしておくことが重要です。例えば、倉庫の保管効率が悪くスペースロスが生じている場合、保管効率を考慮した改善を行う必要があります。
しかし、スペースロスには平面的なロスや高さのロス、山欠けロスなどがあるので、具体的にどのようなスペースロスが生じているのかを明確にして対策をすることが重要です。
このように、現状でどのような課題を抱えているのか明確にすることで、より緻密な改善策を取れるということです。
業務工程を確認する
次に、倉庫内の業務工程を全て確認して、どのような部分に改善が必要なのかチェックしてみましょう。例えば、倉庫内の作業には、入荷や入庫、保管に出庫、梱包に出荷という工程が存在します。
これらの各工程において、どのようなスペースが必要になってくるのかをチェックしておくことが重要です。業務のボリュームに応じて最適なスペースを確保しつつ、決めていくことが重要です。
倉庫レイアウトを決める
基本的にレイアウトは一筆書きの動線が良いとされており、I型レイアウトとU型レイアウトを採用するのが一般的です。それぞれに特徴があるので、どちらが現場に適しているのかを判断してみましょう。
I型レイアウトというのは、入り口から出口まで一直線に進んで業務工程をこなしていくレイアウトになります。直線的な配置のレイアウトなので、基本的にデッドスペースも少なく済むメリットがあります。
一方のU型レイアウトは、入り口と出口が同じ面に配置されており、Uの時を描いた動線のレイアウトになります。U型レイアウトは、比較的有効面積の少ない倉庫でも活用できるメリットがあります。
保管場所を決める
倉庫レイアウトが決まった場合、次は実際にどのような場所に商品を保管するのかを決めていきましょう。この際に活用するのが、前項でも解説したABC分析やロケーション管理という考え方です。
取り扱い業種にもよりますが、例えば商品の出荷頻度に応じたABC分析を行い、それに準ずる形の保管場所を決めておきましょう。作業効率や動線を最適化した保管方法にすることで、業務改善していくことが重要です。
倉庫レイアウト例
倉庫の配置は主にI型とU型に分けられます。この二つの主な違いは、入出庫口の位置にあります。I型では、入庫口がある側と反対側に出庫口が配置されています。一方、U型では、入出庫口が同じ場所にあるか、同じ壁面に二つ設けられています。それぞれのタイプについての具体的なレイアウトを見てみましょう。
I型タイプのレイアウト例
I型タイプの倉庫レイアウトは、入庫から出庫までの一連の流れが効率的で、広い保管スペースを提供します。しかし、作業員が同一ラインに集中しやすいというデメリットがあります。これを解消するためには、広い作業と移動エリアを確保し、作業員間の動線が交差しないよう配慮することが重要です。
さらに、このタイプのレイアウトでは、作業員の移動距離を最小限に抑えるため、出荷頻度が高い商品を中心に配置することが鍵です。中央部分から外側に向かって、出荷頻度が高い商品から低い商品へと配置することで、効率的な作業環境を実現できます。
U型タイプのレイアウト例
U型タイプの倉庫レイアウトでは、作業員が行き交うことが少なくなるので、I型に比べて作業員がぶつかるリスクは少なくなります。その結果、通路を狭めても大丈夫で、より多くの商品を保管できるスペースを作れます。倉庫の壁沿いに商品を置いて、中央部分を作業エリアにすることで、I型よりも広い作業スペースを持てます。
また、U型では、出入り口の近くによく出荷される商品を置くことで、作業員の移動距離を短くできます。
ただし、出入り口が同じ場所か同じ壁面にあるので、そこにだけ出荷頻度の高い商品を置くと作業員がその一箇所に集中し過ぎて、作業の効率が下がる可能性があります。
そんな時は、出荷される頻度が高い商品を倉庫内のいろいろな棚に分散して置くと良いでしょう。作業員の移動距離は少し長くなりますが、全体としては作業がスムーズに進むようになるかもしれません。
まとめ
庫内の業務を効率よく行うためにも、非常に重要な要素の一つがレイアウトです。適切なレイアウトにすることで、業務の効率化やコスト削減はもちろんのこと、予期せぬ事故なども防ぐ効果が期待できます。
なお、ABC分析やロケーション管理を考慮して、最適な動線に設計することが必要です。その上で、庫内における各業務の効率を改善していきましょう。
APTでは、倉庫レイアウトのご相談から自動倉庫の新設から設備・システムの更新やリニューアル、点検・保守倉庫のコンサルティングまで幅広いサービスを提供しております。倉庫に関することなら、お気軽にご相談ください。