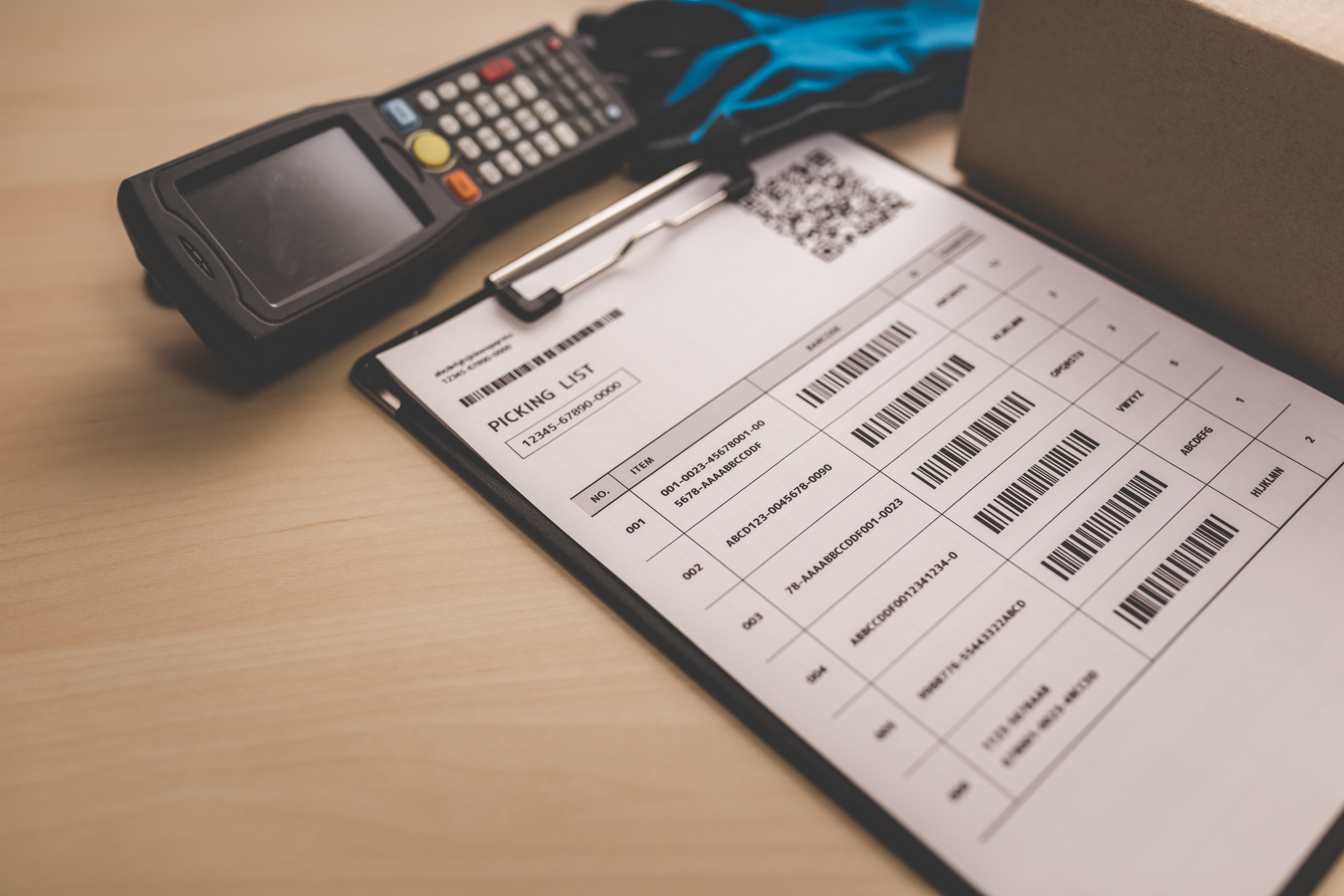
出荷ミスやクレームの要因になりやすい要素といえば検品作業で生じるミスです。製造・物流現場ではこのミスをいかに減らすかが、品質と顧客満足度を守るために重要な要素となります。
そこで本記事では、検品作業ミスの主な原因を整理したうえで、現場ですぐに取り入れられる6つの防止対策を具体的にご紹介します。業務品質の改善に取り組んでいる企業は、ぜひ参考にしてみてください。
目次
検品作業ミスが起こる原因
検品は一見単純な作業に思われがちですが、実際の現場では多くの要因が絡み合い、ミスが発生しやすい工程でもあります。特に人手による作業が中心となる場合、環境や作業負荷、体制の不備などがヒューマンエラーにつながることが少なくありません。
そこでここからは、現場でよく見られる検品ミスの具体的な原因を4つに分けて解説します。
ヒューマンエラーの発生
検品作業の多くは人の目と手に頼っており、集中力の低下や思い込みによってミスが発生しやすい工程です。例えば、長時間同じ作業が続くと人は注意力が散漫になりやすく、見落としや誤認が起こる原因となります。
また、作業者のスキルや経験に依存する場面も多く、判断基準のばらつきによって品質に差が生まれる可能性もあります。こうしたヒューマンエラーは完全には避けられないため、作業環境や仕組みで補う対策を講じることが大切です。
一人当たりの負担が多い
人手不足や業務の効率化を目的とした省人化が進む一方で、現場では一人あたりが担当する検品業務の量が増加するケースがあります。時間内に処理しなければならない件数が多くなるとスピード重視の作業になりがちで、確認の精度が落ちる原因になります。
また、検品以外の業務と兼任する場合、業務間の切り替えによって集中力が低下するため、ミスが生じやすくなります。そのため、作業者の負担に配慮した体制づくりがミス防止の観点からも重要です。
ポジションの配置が最適でない
検品作業が行われる現場のレイアウトが非効率だと、作業負担が偏ったり、物の受け渡しに混乱が生じやすくなります。例えば、作業ラインが長すぎる、視界が遮られている、動線が複雑といった状況では、検品ミスのリスクが高まります。
こうした環境では検品者が本来の確認作業以外にも気を配らなければならず、結果として注意力が分散されます。そのため、ポジションの配置を見直し、無駄な動きを減らすことで、作業の正確性を向上させることが大切です。
確認すべきポイントが多すぎる
検品項目が多すぎると作業者にかかる負担が増え、見落としや確認ミスが発生しやすくなります。外観、数量、型番、ラベル、バーコードなど、多くのポイントを短時間でチェックする必要がある場合、優先順位が不明確だと判断ミスを誘発します。
また、マニュアルが複雑だったり基準が曖昧な場合、作業者ごとに判断が異なり、品質のばらつきにもつながります。そのため、確認項目を絞り、明確化することがミス防止には効果的です。
検品作業ミスの防止対策6選!
検品ミスは人の注意力だけでは完全に防ぐことはできません。だからこそ、現場で実行できる仕組み化による対策が重要になります。
そのため、ここからは業務の標準化から人材育成、環境の改善、そしてシステム導入まで、すぐに取り入れられる6つの具体的な対策を紹介します。
検品マニュアルの整備
検品作業の属人化を防ぐには、誰が行っても同じ品質で確認できるようにマニュアルを整備することが重要です。チェックポイントを明文化し、作業手順を標準化することで、作業者の判断ミスや確認漏れを防げます。
図や写真を使った視覚的な資料を用意すれば、新人でも即戦力として対応しやすくなります。また、マニュアルは定期的に見直し、実際の現場状況と乖離がないよう更新を続けることも大切です。
ダブルチェック体制の導入
検品作業にダブルチェックを導入することで、1人の見落としをもう1人が補う体制を構築できます。重要な出荷物や高額商品では、2人以上の確認工程を設けることで、人的ミスのリスクを大幅に低減できます。
ただし、形式的な確認に陥らないよう、担当者の役割やチェック項目を明確にし、責任意識を持って取り組める体制づくりも必要です。適切なチェック体制は業務品質が向上するため、総じて顧客満足度も向上するでしょう。
作業者の教育・スキルの平準化
作業者の経験値や判断力に差があると、検品の品質にもバラつきが生じます。そのため、教育を通じてスキルの平準化を図ることが重要です。新任者へのOJTに加え、定期的な研修やテストを実施することで、基準に沿った作業ができるようになります。
また、不良事例やクレーム事例を共有することで、実践的な理解が深まり、ミスを未然に防ぐ意識づけにもつながります。このように、継続的な教育体制によって組織全体の品質レベルを底上げすることができます。
作業環境の見直し
検品精度は作業者の能力だけでなく、作業環境にも大きく左右されます。例えば、作業スペースが狭いと物品の混在や取り違えが起きる可能性があります。また、類似した商品を同じ場所で管理すると、商品の取り間違いが発生する可能性が高まります。
そのため、検品ラインの動線や作業台の高さ、周囲の騒音や温湿度など、作業者が集中しやすく取り間違いをしにくい環境を整えることが大切です。定期的な現場点検と改善を繰り返すことで、環境要因によるミスを最小限に抑えられます。
専用システムの導入
属人的な検品を脱却するには、専用システムの導入が効果的です。例えば、バーコードやQRコードの読み取りによる自動照合、AI画像認識による不良検知などを活用すれば、ミスの起こりにくい仕組みを構築できます。
これにより作業スピードと正確性を両立しつつ、トレーサビリティも確保できます。また、WMSなどの物流システムと連携すれば、検品から在庫管理、出荷まで一元的な品質管理が実現できるので、倉庫内業務全体の最適化も実現させることができます。
アウトソーシングの活用
社内リソースが不足している場合や、大量の検品作業が短期間で発生するケースでは、外部の専門業者へのアウトソーシングも効果的です。専用の設備と経験豊富な人材を持つ業者に任せることで、安定した品質と効率的な運用が期待できます。
また、第三者による客観的なチェックは、社内だけでは気づきにくい問題点の発見にもつながります。ただし、業務を外注に任せることで自社にノウハウがたまりにくくなるため、メリットデメリットをきちんと把握した上で判断することが大切です。
まとめ
検品時における作業ミスというのは、出荷トラブルやクレームに直結する重大な業務ミスになります。多くの現場ではヒューマンエラーや作業負担の増加、環境要因などが重なりミスが発生しやすい状態にあります。
しかし、マニュアルの整備やチェック体制の強化、作業環境の見直し、専用システムの導入など、実践的な対策を講じることでこれらのミスは大幅に削減可能です。また、自社だけで対応が難しい場合は、アウトソーシングも視野に入れながら、仕組みとして検品の精度を高めていくことが重要です。
関連記事
検品作業を自動化するメリットやおすすめの自動化システムを紹介
誤出荷を防止するためには?対策ポイントやおすすめのシステムをご紹介