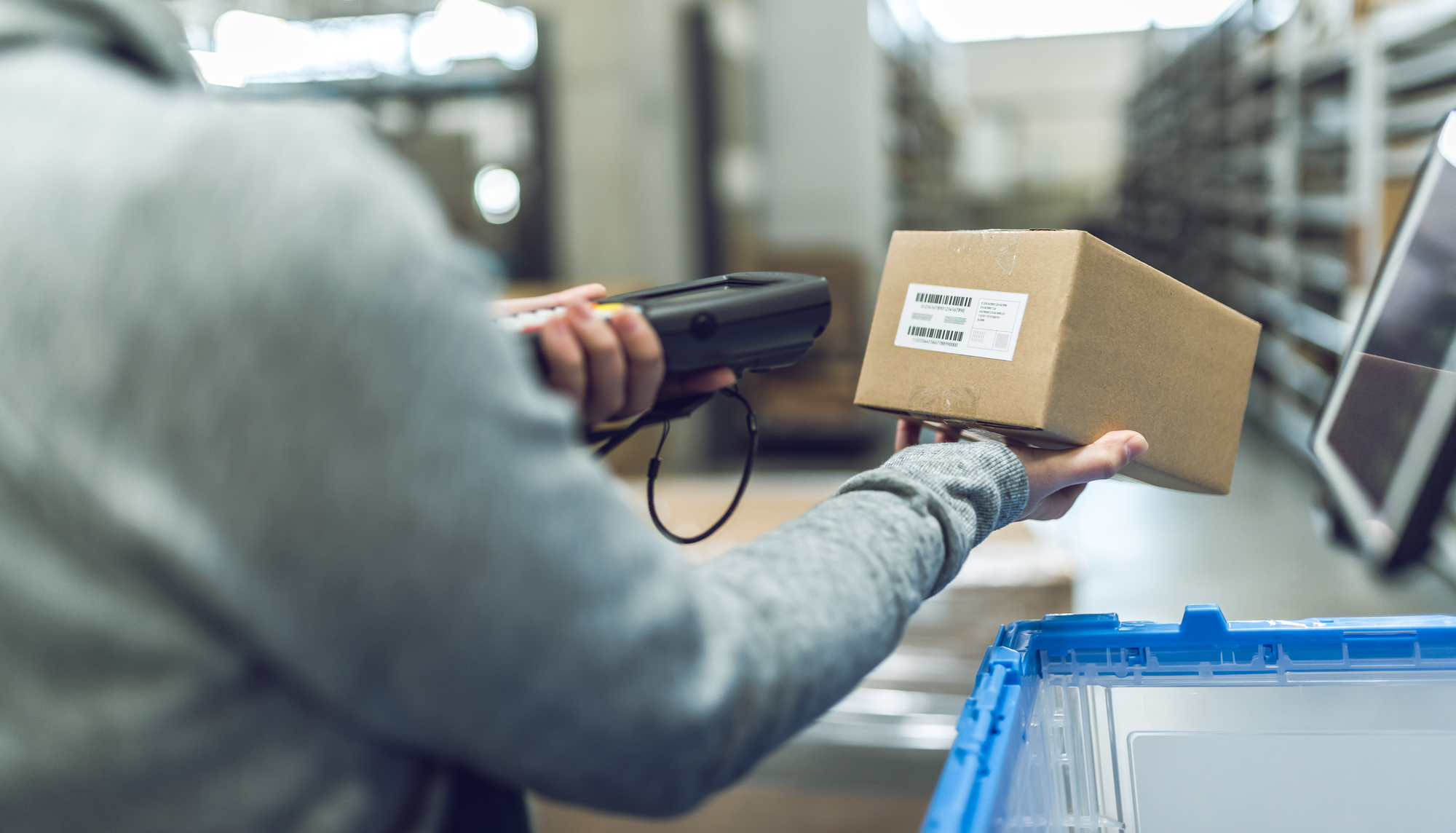
保管されている商品を出荷指示に応じてピックアップするピッキングには、いくつかの種類が存在します。なかでもトータルピッキングはまとめて商品をピッキングできるため、効率の良い方法として活用されています。
そこで今回の記事では、ピッキングの中でもトータルピッキングに焦点を当てて解説します。トータルピッキングのメリットやデメリット、効率化するためのシステムなどを紹介しますので、ぜひ参考にしてみてください。
目次
トータルピッキングとは?
トータルピッキングとは、さまざまな注文を受けた際に商品をまとめてピッキングできる手法の一つです。別名で「種まき方式」や「総量ピッキング」とも呼ばれており、複数ある出荷先をまとめてピッキングしたい場合に適している方法になります。
出荷先の件数が多くSKU数はそれほどでもないというようなケースの場合、トータルピッキングによる方法が効率的になります。そのため、比較的出荷先が多いという場合は、この方法を採用してみましょう。
トータルピッキングのメリット
トータルピッキングのメリットは以下のとおりです。
- 移動時間の短縮で作業効率が向上する
- 数量検品も同時に行える
- 人員削減によるコストカットが可能
ここからは、上記に挙げた各メリットの詳細を解説します。
移動時間の短縮で作業効率が向上する
トータルピッキングを採用することで、商品探しの移動時間を短縮して作業効率を向上させることができます。この方法でピッキングを行えば、商品を保管している場所から仕分けをする場所への移動を少なくできるメリットがあります。
そのため、ピッキング作業における移動のロスを削減し、業務効率が向上するというわけです。出荷先毎にピッキング作業した場合、その都度移動をしなければなりませんが、この方法なら効率よく移動のロスを削減できます。
数量検品も同時に行える
トータルピッキングを採用することによるメリットは、数量検品も同時に行えるという点です。この方法なら一気にピッキングを行えるほか、オーダー別に仕分けを行って残量に誤差が出なければ数量に間違いがないことを確認できます。
そのため、この方法というのは、数量検品における工程をより効率的に行える方法でもあるということです。ただし、出庫をする際には別途検品を行って正確性を担保するケースも多い傾向にあります。
人員削減によるコストカットが可能
トータルピッキングで作業を行えば業務の効率化を実現できるので、人員削減によってコストカットを実現させることができます。昨今は物流業界を始めさまざまな業界で人手不足が問題になっているため、人員を削減できれば人材不足の問題も解消するでしょう。
また、人件費削減によるメリットも非常に大きい一面があります。例えば、採用するためのコストや人材育成のコストなど、関連するコストも削減することが可能です。このように、人削減によってコストカットを行うことで、人件費以外のさまざまなコストも削減できるメリットがあります。
トータルピッキングのデメリット
トータルピッキングのデメリットは以下のとおりです。
- 作業の工程が増加する
- スペースを確保する必要がある
メリットの多いトータルピッキングにも、デメリットになり得るポイントがいくつか存在します。導入後に作業効率が落ちてしまわないためにも、どのようなデメリットがあるのかを確認しておきましょう。
作業の工程が増加する
トータルピッキングの場合、作業の工程が増加してしまうデメリットがあります。例えば、シングルピッキングの場合、ピッキング作業の後は検品と梱包の工程を経たら完了になります。
一方で、トータルピッキングの場合、ピッキングの後に検品を行い、仕分け作業を経て再度検品を行って梱包工程に移ります。このように作業工程がシングルピッキングよりも増えてしまうという点は、この作業法によるデメリットといえるでしょう。
スペースを確保する必要がある
作業スペースを確保する必要があるという点も、トータルピッキングにおけるデメリットといえます。トータルピッキングというのは、ピッキングを行う作業スペースと仕分け作業をするスペースの2エリアを確保しなければなりません。
そのため、倉庫内で限られたスペースしか確保できないような場合、トータルピッキングでは作業効率が落ちてしまう可能性もあります。そのため、この方法を活用する際には、倉庫内のレイアウトも含めて導入検討をする必要があるということです。
以下の記事ではピッキングシステムについて詳しく説明しております。
トータルピッキングを効率化する方法
トータルピッキングを効率化する方法は以下のとおりです。
- マニュアルの見直し
- 動線の見直し
これらのポイントに注意することで、より作業を効率化させることができます。業務効率を上げていくためにも、トータルピッキングではどのようなポイントに注意すべきかを確認しておきましょう。
マニュアルの見直し
作業のマニュアルを見直すことで、業務の効率化を実現できる場合があります。例えば、ピッキング作業におけるルールを明確に定めた上で、スタッフに周知徹底することで業務効率を上げることができます。
ピッキング作業は人の手を介して行うことが多いので、非常に属人的になりやすい傾向にあります。そのため、作業ルールやマニュアルなどを見直してみることで、業務改善を図れる可能性があるわけです。
また、マニュアルで業務の標準化を実現できればヒューマンエラーも少なくなるので、業務品質が向上します。
動線の見直し
作業の動線を見直すことで、業務効率を改善できる可能性があります。ピッキングにおいて作業時の移動はロスも生じやすく、業務を効率化させる上では無視できない要素ともいえます。
例えば、商品探しの際にすぐに見つけられるように工夫したり、必要なモノ以外を置かないなどして動線を簡略化していくことが重要です。また、出荷のレベルや頻度に応じて配置を変更するといった工夫も必要になるでしょう。
トータルピッキングを効率化するシステムを紹介
トータルピッキングをより効率化するためには、以下のようなシステムが効果的です。
- ゲートアソートシステム
- 倉庫管理システム
ゲートアソートシステムとは、トータルピッキングをより効率化するためのシステムです。パーコードで読み取った情報を元に商品の保管ゲートが開くため、作業ミスも減り業務の効率化を実現できます。
また、倉庫管理システムを導入すれば、入出庫、在庫情報、ロケーション管理なども行えるほか、帳票なども発行することが可能です。デジタルでリアルタイム管理することができるので、ヒューマンエラーもなくなり業務効率が向上します。
このようにシステムを活用することで業務の効率を格段に向上させることができるので、積極的に活用していきましょう。
以下の記事では自動ピッキングロボットについて詳しく説明しております。
自動ピッキングロボットの種類や導入メリット、デメリットを解説
まとめ
トータルピッキングというのは、出荷先が多い場合に適しているピッキング方法です。ピッキング作業というのは属人的にもなりやすく、ヒューマンエラーも起こりやすい工程の一つです。
そのため、ゲートアソートシステムや倉庫管理システムなどを活用しつつ、より正確で効率的なピッキング作業を実現させましょう。
APTでは、ピッキングシステムをはじめ、物流倉庫内で行われる「保管・搬送」などといった作業の自動化&省人化を目的とした自動化システムを提供しております。お気軽にお問い合わせください。